Gear Manufacturing Process Step by Step
In this article, I am going to discuss gear manufacturing processes. For the gear manufacturing process, the most important thing is gear materials. However, the surface finish of the gear wheel, process cost, gear type, quantity, and quality is very important. According to the gear materials manufacturing process will be changing, for instance, we can manufacture plastic gear by using injection molding, and for metal gear wheels we can go for machining.
Common Gear Materials for Gear Manufacturing
Gear material is not a single term. It has enormous verity according to the design requirement, the strength of the gear wheel, environmental conditions, reliability, and fatigue life. Following are the basic gear materials.
- Cast Iron
- Steel(Nitride and Carburizing)
- Aluminum
- Bronze
- Brass
- Plastic
Other than these you can select different engineering materials according to your requirements. After selecting gear material you have to select the most appropriate gear manufacturing process.
Basic Manufacturing Process Steps
There are a lot of methods for gear manufacturing. The followings are the basic steps.
- Firstly perform the blank with or without gear tooth
- The Heat Treatment process for the gear blank if it’s required
- Secondly machining the gear blank to get the appropriate dimensions
- Finish the preform teeth or produce the gear teeth by machining
- Harding process for the gear teeth or all gear wheel
- Thirdly final finishing of the gear teeth(shaving, grinding)
- Final inspection of the gear wheel
Other than these basic steps there are some special manufacturing methods for gear manufacturing, for instance, injection molding for plastic gear wheels can identify as a different process.
What you need to consider when select a process?
Before selecting a gear manufacturing process you have to think about the following criteria according to your gear requirements and design requirements.
- Gear Material for design requirement
- Gear Types and Power transmission requirement
- Cost Requirement and Quantity of Batch Production
- Machine setup cost and unit cost of the gear wheel
- Quality and Finishing or gear wheels
Considering these factors you can select the best gear manufacturing processes. The common procedure is, firstly you can select forming process for gear blank manufacturing. Secondly, you can select a gear machining process for gear teeth. Finally, you can select a gear finishing process for more accurate and quality gear teeth.
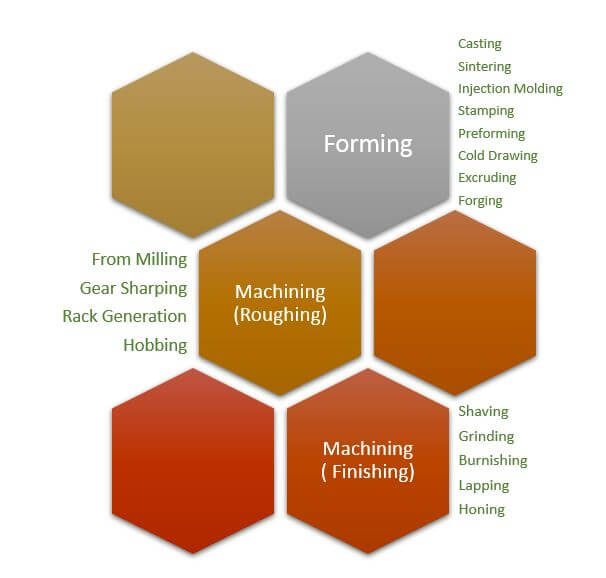
Selection of gear forming process
The forming process is very suitable for high-quantity production. Basically, the quality and finishing of the gear depend on mold and die quality. The initial cost is very high for the die and mold. The accuracy of the gear teeth depends on the quality of the die and mold but the required quality can be obtained after forming roughing and finishing operations. There are a bunch of manufacturing processes for gear manufacturing.
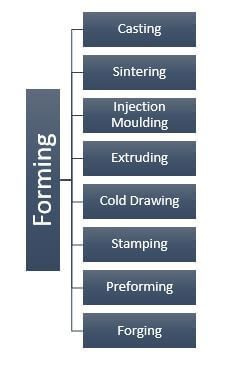
Casting Process
The casting is not a single process. You can select Sand casting, Die casting, Metal Mold casting, Investment casting, Shell mold casting, and Centrifugal casting according to your requirement. However, casting is a basic process for forming gear blanks. After that, you can go for teeth matching and finishing processes.

Sand Casting :
Sand Casting can be used as two methods. You can use sand casting for blank gear wheel production or you can use sand casting as complete gear manufacturing with gear teeth. But the surface finish of the sand casting is very low. The followings are the applications and characteristics of sand casting.
Characteristics:
- Responsible costs for products and tools
- Gears are very noisy due to backlash
- Low precision and low surface finish
- Dimension accuracy is very less
- Not suitable for critical applications
Applications:
- Toys
- Small Appliances
- Dam gate hoisting gearbox
- Hand Operated cranes
- Automobile and truck transmissions
Materials for Sand Casting:
- Cast Iron
- Bronze
- Brass
- Magnesium Aluminum
- Zinc
Die Casting
Die casting is a very important gear manufacturing process for Non-ferrous gears. Hot Chamber Die casting and Cold Die casting processes can be used for the gear die casting. Therefore you can use these methods to manufacture all types of gears.
Characteristics:
- High-quality surface finish and accuracy
- High production quantities are possible
- Tooling cost is high
- Better for the small size of gears
Applications:
- Cameras
- Small Speed reducers
- Gear Pumps
- Washing machines
Materials for Die casting:
- Brass
- Aluminum
- Zinc
Investment Casting
The investment casting process is more suitable for small-size and medium-size gear wheels. The quality of the investment casting gear wheels can be improved by using the surface finishing technique.
Materials for Investment Casting:
- Beryllium Copper
- Tool Steel
- Monel
- Nitriding Steel
Metal Mold Casting
You can select metal mold casting for medium-size gear manufacturing. During the metal mold casting, accuracy and finishing are very low. But you can improve the gear wheel quality by using several machining and surface treatment processes.
Centrifugal Casting
Other than the metal casting centrifugal casting can use for manufacturing blank gear rims. This method is very suitable for worm gears. The most common materials for centrifugal casting are Cast iron and phosphor bronze.
Sintering Process
The sintering gear manufacturing process is a powder metallurgy process. Using this process we can produce high-quality gear like die casting, therefore no need to do any finishing operation for the sintering process.
Characteristics :
- Can manufacture high-quality gear wheels.
- Possible to manufacture various types of gear wheels including helical gears and a combination of gears.
- The secondary machining process is not required.
- Keyways can be manufactured with the gear.
Injection Molding
Injection molding is a very common plastic manufacturing process. This process can be used for gear manufacturing as well. You can select Non-metallic thermoplastics materials for this process.
Characteristics:
- Low precision and small version of gear wheels
- Can use without lubricant
- Possible for very large production
- Low cost but the initial tooling cost is very high
- Common applications are toys, plastic gear motors, Etc
Material for injection molding gear manufacturing:
- Nylon
- Cellulose acetate
- Polystyrene
- Polyimide phenolic

Extruding
You can use the extruding process to form a long rod with gear teeth. After the extruding process, long rad can size into the required sizes. Then you can make a bore for the gears and required finishing processes. But this process is very suitable for Non-Ferrous materials like aluminum and copper gears. Extruded gear wheels have a good surface finish and good strength due to a pore-free dense material structure.
Materials for the extruding process:
- Phosphor bronze
- Naval brass
- Copper
- Aluminum
Cold Drawing
In the cold drawing process, a metal rod draws a through-hardened die to form the gear teeth for that rod. The main feature of these gear wheels is high strength and low ductility. After that, you can apply the finishing operations for the gear wheels.
Stamping
Stamping is a sheet metal process and this manufacturing process can use for gear manufacturing. High production quantities are possible with this process. But accuracy and surface finish is very poor.
Selection of gear machining process
After the blank forming process, you can go for the gear machining process. Using the gear machining process you can obtain gear teeth, bore or keyholes, and finishing. The followings are basic and common gear machining process.

From Milling Process
This method is very slow speed and fiar accurate process. Common cutting tools are disk cutters and end milling tools. However, milling is very suitable for small production and fiar accuracy requirements.
Gear Shaping Process
Special shaping machines use for this process and blank forming metal parts are rotated around the shaping tool. The accuracy of the gear tooth is very high. But dimension error of the shaping tool is directly transferred to the gear wheel. Internal gear wheels can be produced by using this method.
Rack generation
For this process gear, tooth shape rack is used. Blank formed gear wheel (Without gear tooth) is used for generating the gear teeth. This method is less accurate than the gear shaping and gear hobbing process.
Gear Hobbing
Gear hobbing is the process more common process in the gear manufacturing industry. Accuracy and surface finish are very high and tool errors are compensated due to the hobbing tools. Hob is rotating normally to the gear blank and make gear teeth.
Selection of gear finishing methods for gear manufacturing
Gear finishing is the final stage of gear manufacturing. You can select the suitable process according to the gear material, black manufacturing process, and machining process of the gears. followings are the most common finishing process.

Shaving process
The shaving process can use to gear the better surface finish for the gears and correct the profile errors. In this process, the shaving tool meshes with the gear wheel at high rpm to get the required finish.
Grinding
The most common method is the use of the grinding wheel to get the surface finish. The computer control grinding wheel run over the gear teeth.
In addition to shaving and grinding processes, burnishing, lapping, and honing are surface finishing techniques of gear wheels. Usually, horning machines are used for this process.
In conclusion, gear manufacturing is a three-step process. Which are black forming, machining, and finishing operations. Above all steps have several processes. But you have to select the manufacturing process according to your requirements. However, you have to think about the materials as well. Hope you all get a better understanding of gear manufacturing.
Really appreciate, taking the time to read the article about the gear manufacturing process. So keep in touch with MechHeart and feel free to add some comments here and share your knowledge with us.
GD&T Symbols for Engineering Drawings
GD and T is stands for Geometric Dimensions and Tolerances. Most of the engineering fields are using different types of…
Surface Finish Symbols for Engineering Drawings
Surface finish symbols are needed to represent the surface texture requirement to manufacturers. If you are working on CNC machining…
Best CAD Software for Mechanical Product Design
Product Designing is an important marketing factor in different industries. For instance, Mechanical Products, Fashion Designing, Civil, Electrical, Chemical, Material,…
CNC and NC Machines for Industrial Applications
CNC machines are playing very impotent role in today’s manufacturing industry. CNC Milling, Lathe, Drilling, Welding and Various Cutting Machines…
MEMS and NEMS Devices and Their Applications
MEMS and NEMS are the short forms of the Micro Electromechanical Systems and Nano Electromechanical Systems. NEMS is a class…
Different Types of Gears and Their Uses
Different types of gears include spur gears, helical gears, bevel gears, worm gears, and planetary gears, each having unique characteristics…
Gear Manufacturing Process Step by Step
In this article, I am going to discuss gear manufacturing processes. For the gear manufacturing process, the most important thing…
What is a Cutting Tool for Precision Machining?
A cutting tool is a type of instrument designed to cut or shape various materials, especially wood, plastic, and metals….
What is a Belt Drive in Power Transmission?
A belt drive is a well-known mechanism that uses belts to transmit power or motion between rotating shafts. You may…
The Life-Changing Future of the Prosthetic Hand Development
Prosthetic hands are not just engineering designs; they are always a sensitive topic for those requiring them. A prosthetic hand…
Isometric Projection in Engineering Drawing
There are various methods used to present objects in both 2D and 3D views. One of the common types of…
What is CNC Programming?
CNC programming is also known as Computer Numerical Control programming. Basically, the process of creating instructions or code is called…
What is the Difference between Sheet and Plate?
Sheets and Plates are not uncommon words. Everyone knows about sheet metal and metal plates. But actually, do you know…
What is the Difference between Bolt and Screw?
Bolts and Screws are common fasteners in many industries. In the manufacturing and construction industry, widely use both screws and…
Orthographic Projection in Engineering Drawing
Orthographic projection in engineering drawing is the essential technique for accurately representing three-dimensional objects on a two-dimensional plane. Engineers rely…
0 Comments