Gear Manufacturing – Plastic Gears
Plastic gears have become an increasingly popular choice in various industrial applications due to their lightweight, corrosion resistance, and cost-effectiveness. The manufacturing process for plastic gears involves several key steps, starting from the selection of the right material and design to the actual production of the gear, and the final surface finishing and quality control. Depending on the specific requirements of the application, plastic gears can be produced through a range of manufacturing processes. Injection molding, extrusion molding, compression molding, and CNC machining are the some of common manufacturing processes. The goal of this article is to provide a comprehensive overview of the gear manufacturing process for plastic gears, highlighting the key considerations, challenges, and techniques involved in each step.
Materials Selection for Plastic Gears
The selection of the right material is a critical step in the gear manufacturing process for plastic gears. Different types of plastic materials offer different properties, such as;
- Strength
- Durability
- Wear Resistance
- Dimensional stability
These are considerable factors when we are selecting plastic gears for a particular application. The most commonly used materials for plastic gears include:
- Acetal (POM) – A strong and rigid material with low friction, making it ideal for applications requiring high precision and accuracy.
- Nylon – A versatile and durable material that offers good wear resistance and low friction, making it ideal for high-load applications.
- Polycarbonate (PC) – A lightweight and impact-resistant material that offers good dimensional stability and transparency, making it ideal for applications that require visibility and clarity.
- Polypropylene (PP) – A cost-effective and lightweight material that offers good chemical resistance, making it ideal for applications in harsh environments.
When selecting a material for plastic gears, it is important to consider factors such as;
- Operating Conditions
- Load Requirements
- Environmental Factors
These factors need to ensure that the material is suitable for the specific application. A material that performs well in one application may not be suitable for another. The selection process may also involve trade-offs between cost, performance, and manufacturability, and should be based on a careful analysis of the specific requirements of the application.
Design and Engineering Considerations for Plastic Gears
Design and engineering considerations play a crucial role in the manufacture of plastic gears. They impact the performance and reliability of the gears in the final application. Some of the key design and engineering considerations for plastic gears include:
- Load capacity – The load capacity of the gear is a critical factor that affects the size, shape, and material of the gear.
- Tooth geometry: The tooth geometry of the gear, including the number of teeth, pitch, and profile, affects the smoothness and efficiency of the transmission of power.
- Gear accuracy – The accuracy of the gear is a critical factor that affects the performance and reliability of the transmission of power.
- Surface finish – The surface finish of the gear affects the friction and wear resistance of the gear.
- Manufacturing constraints – The design of the gear must also take into account the constraints of the manufacturing process, such as molding capabilities and material properties.
Design and engineering considerations impact the performance and reliability of plastic gears, so must be carefully evaluated and incorporated into the design. This includes load capacity, tooth geometry, accuracy, surface finish, and manufacturing constraints to ensure the gear meets specific application requirements.
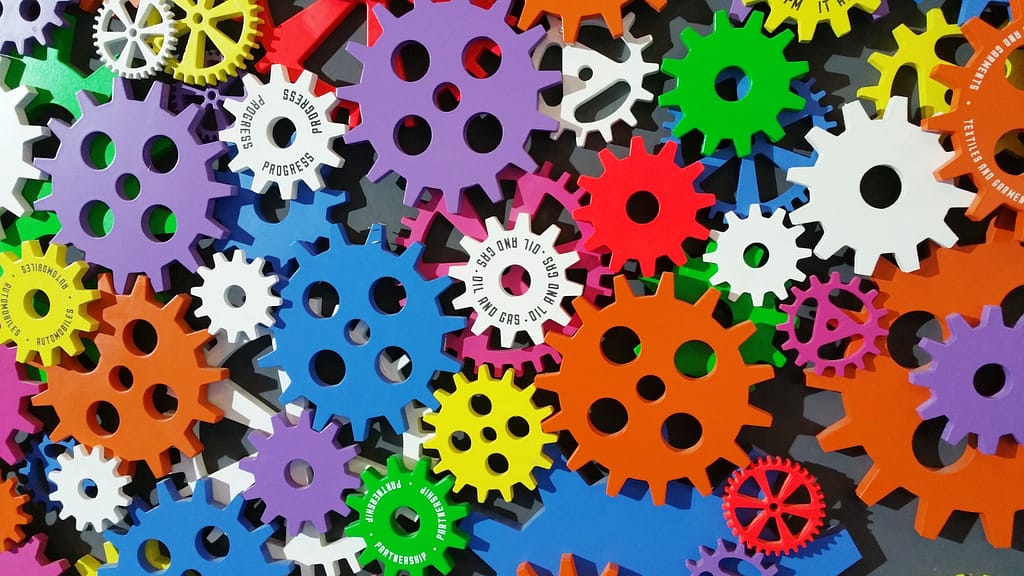
Plastic Gear Manufacturing Process
Most of the time plastic gears are manufactured by using the molding process and other than the molding process CNC operations are also involved for some special applications.
- Injection molding
- Extrusion molding
- Compression molding
- Transfer molding
- Rotational molding
Injection Molding for Plastic Gear Manufacturing
Injection molding is a widely used method for producing large quantities of plastic gears in a single cycle. This method involves melting the plastic material and injecting it into a mold under high pressure. The material cools and solidifies in the mold to form the final gear shape.
Injection molding is ideal for producing gears in high volumes. The injection molding process is highly efficient and allows for the production of large numbers of gears in a short amount of time. The process is also highly automated, with minimal manual intervention required, which results in consistent quality and uniformity of the gears produced.
Another advantage of injection molding is that it allows for the use of a wide range of materials, including
- Thermoplastics
- Thermosets
- Elastomers
The process also enables the production of gears with complex shapes, intricate details, and high accuracy. Making these gears are ideal for applications that require precise and high-quality gears.
Injection molding for plastic gear manufacturing has high tooling costs and requires specialized equipment and expertise. Careful design and planning are necessary to meet performance and reliability specifications and minimize waste and costs.
Extrusion Molding for Plastic Gear Production
Extrusion molding is a method of producing plastic gears by forcing melted plastic material through a die to create a continuous gear profile. The resulting gear profile is then cut to the desired length to form individual gears.
This method is highly efficient and can be used to produce gears in high volumes, making it ideal for mass production. Extrusion molding also allows for the use of a wide range of materials, including thermoplastics. Thermoplastics are ideal for gears due to their high strength, low weight, and durability.
Extrusion molding is suitable for plastic gears with complex shapes and profiles and results in gears with uniform cross-sections and consistent quality. It is ideal for high-accuracy and precision applications.
Extrusion molding for plastic gear production requires specialized equipment and expertise. The process has limitations for intricate details and high surface finish. Careful design and planning are necessary for gears to meet performance and reliability specifications and minimize waste and costs.
The Role of CNC Machining in Plastic Gear Manufacturing
CNC (Computer Numeric Control) machining plays a crucial role in plastic gear manufacturing, as it is used to produce high-precision gears with complex shapes and intricate details. In CNC machining, a computer program is used to control a machine tool, such as a lathe or mill, to produce the gear.
CNC machining produces high-precision plastic gears with tight tolerances and consistent quality. It is important in plastic gear manufacturing for proper gear mesh and optimal performance.
Additionally, CNC machining allows for the production of gears with intricate shapes, features, and details, such as teeth, bosses, and other features, which would be difficult or impossible to produce using other methods. This makes CNC machining a versatile solution for a wide range of plastic gear applications.
CNC machining is more expensive and time-consuming compared to other plastic gear manufacturing methods. Careful design and planning are necessary for gears produced using CNC machining to meet performance and reliability specifications and minimize waste and costs.
Surface Finishing and Post-Processing for Plastic Gears
Surface finishing and post-processing are important steps in the plastic gear manufacturing process to improve the appearance, functionality, and durability of the gears. This can include operations such as;
- Polishing
- Sandblasting
- Electroplating
- Anodizing
- Painting
The specific surface finishing techniques used will depend on the requirements of the specific application, including factors such as wear resistance, corrosion resistance, and thermal stability. Proper surface finishing and post-processing can help to ensure that the gears perform as expected and meet the desired specifications.
Cost Considerations and Economic Benefits of Plastic Gear Manufacturing
Cost is a major factor in the plastic gear manufacturing process. Plastic gears often cost less to produce than metal gears because the raw materials are less expensive, energy consumption during production is lower, and tooling costs are lower. Additionally, plastic gears are often lighter and more resistant to wear and corrosion, reducing maintenance and shipping costs. These benefits make plastic gear manufacturing a popular choice in many industries, especially when the cost is a concern. To determine the most cost-effective manufacturing method, it’s important to consider factors like production volume, lead time, and quality level in relation to the specific application requirements.
0 Comments