Spur Gears vs Helical Gears
Spur gears and helical gears are two types of gears used in mechanical systems for power transmission. Understanding the differences between these two types of gear is important for making informed decisions in engineering and design. Spur gears are simple, efficient, and cost-effective, while helical gears offer smoother, quieter operation and higher load capacity. In this article, we will dive into the key differences between spur gears and helical gears and explore the benefits and drawbacks of each. Compare spur gears vs helical gears. Learn the pros and cons, design, operation, and applications of each type. Make the right choice for your project.
There are different Gear Manufacturing Processes and Gear Materials that can use to manufacture both of these gear types. according to your application and requirements, you can decide the gear type and feature and mechanical properties as well. You can select Spur Gear or Helical Gear for your gear design project or you can buy gears according to your requirements.
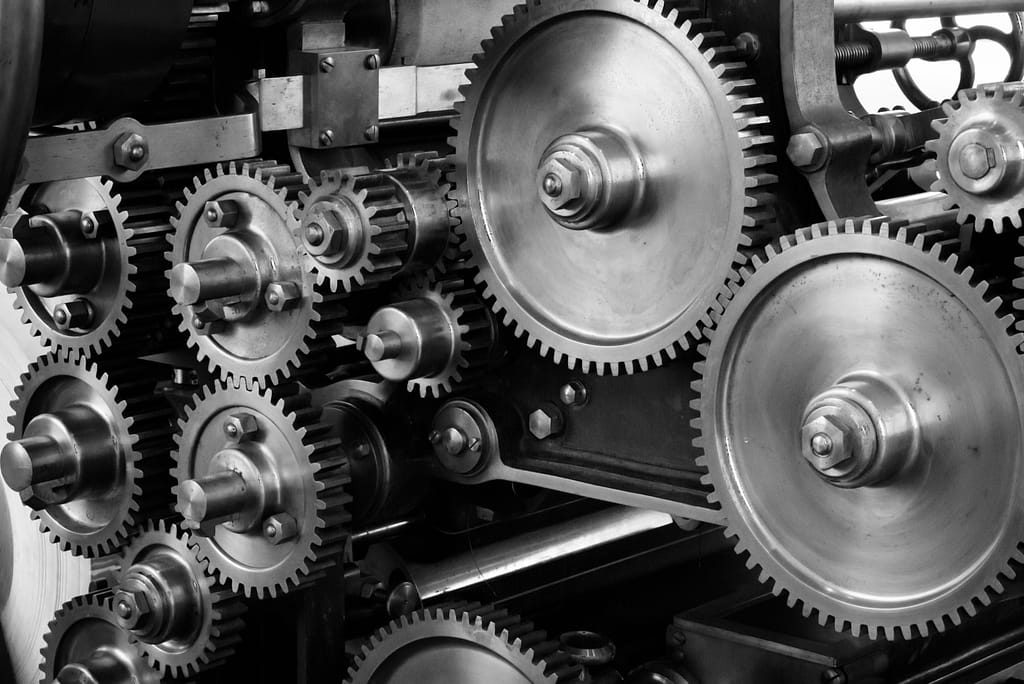
What are Spur Gears
Spur gears are cylindrical gears with straight teeth that are parallel to the axis of rotation. They are the simplest type of gear and are used to transmit rotary motion and power from one shaft to another. They are commonly used in industrial, agricultural, and transportation applications where simplicity, cost-effectiveness, and high speed are required. Spur gears are generally noisy and can generate vibrations, but they are easy to manufacture and have a long service life.
Characteristics of Spur Gears
- Straight teeth: The teeth on spur gears are straight and run parallel to the axis of rotation.
- Cylindrical shape: Spur gears are cylindrical in shape and have a circular cross-section.
- Simple design: They have a simple design and are easy to manufacture, making them cost-effective.
- High speed: Spur gears can operate at high speeds and are commonly used in high-speed applications.
- Noisy operation: Spur gears tend to generate more noise compared to other types of gears, and their operation can be noisy.
- Vibrations: They can also generate vibrations, which can affect the reliability and durability of the system.
- Durable: Despite their potential noise and vibration, spur gears are durable and have a long service life.
What are Helical Gears
Helical gears are a type of cylindrical gear with teeth cut at an angle to the axis of rotation. Unlike spur gears, helical gears offer a smoother, quieter operation, making them ideal for high-load, high-precision applications. The angled teeth of helical gears produce less noise and vibration, and they can handle higher loads compared to spur gears. Despite their increased cost and complex manufacturing process, helical gears are widely used in industries such as aerospace, automotive, and heavy machinery. If you require a reliable, smooth, and quiet power transmission solution, helical gears may be the right choice for your application.
Materials
Helical gears can be made from a variety of materials, each with its own unique properties and advantages. Some of the common materials used for helical gears include:
- Steel: Steel is the most commonly used material for helical gears due to its strength, durability, and affordability.
- Cast iron: Cast iron is a durable and low-cost option for helical gears, although it may not have the same strength and wear resistance as steel.
- Bronze: Bronze is a corrosion-resistant material that is commonly used for helical gears in marine and outdoor applications.
- Aluminum: Aluminum is a lightweight and corrosion-resistant material that is commonly used in aerospace and automotive applications.
- Plastic: Plastic helical gears are lightweight, corrosion-resistant, and have low friction. They are commonly used in applications that require low noise and low weight.
- Stainless Steel: Stainless steel is a corrosion-resistant material that offers high strength and durability. It is commonly used in food processing, medical, and chemical processing applications.
The choice of material depends on the specific requirements of the application, such as load capacity, corrosion resistance, and cost.
What are Helical Gears Used for
Helical gears are used in a variety of applications where smooth and quiet operation, as well as high load capacity, is required. Some of the common uses of helical gears include:
- Heavy machinery: They are commonly used in heavy machineries, such as elevators, cranes, and conveyors.
- Automotive industry: Helical gears can use in automotive transmissions, power steering systems, and differential drives.
- Aerospace industry: They can use in aircraft and spacecraft systems, including gearboxes and actuators.
- Process control: Helical gears can use in process control systems, such as oil and gas pipelines and chemical processing plants.
- Precision instruments: Helical gears are can use in precision instruments, such as laboratory equipment, optical equipment, and medical devices.
Overall, helical gears offer a reliable and efficient solution for power transmission in high-load, high-precision applications.
Spur Gears vs Helical Gears
Spur gears and helical gears are both types of gears that can use for power transmission. But when we compare Spur gears vs Helical Gears there are key differences.
- Teeth Shape: Spur gears have straight teeth that are parallel to the axis of rotation, while helical gears have teeth that are cut at an angle to the axis of rotation.
- Operation: Spur gears tend to generate more noise and vibration compared to helical gears, which offer smoother and quieter operations.
- Load Capacity: Helical gears can handle higher loads compared to spur gears, making them suitable for high-load applications.
- Cost: Spur gears are simple to manufacture and have a lower cost compared to helical gears, which are more complex to manufacture.
- Precision: Helical gears offer higher precision compared to spur gears, making them suitable for high-precision applications.
In conclusion, the choice between spur gears and helical gears depends on the specific requirements of the application, such as noise, vibration, load capacity, precision, and cost. Understanding the key differences between these two types of gears will help make informed decisions in engineering and design.
0 Comments