MEMS and NEMS Devices and Their Applications
MEMS and NEMS are the short forms of the Micro Electromechanical Systems and Nano Electromechanical Systems. NEMS is a class of devices integrating electrical and mechanical functionality on the Nano scale. However Today, MEMS evolved in terms of dimension, creating a new technology named nanotechnology or Nano electromechanical systems (NEMS). In comparison with MEMS which range in size from 20 micrometers to one millimeter, the NEMS components vary between 1 and 100 micrometers.
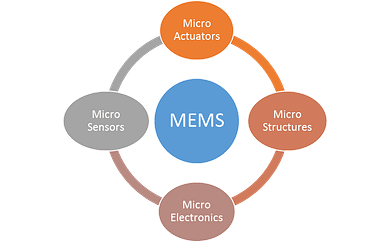
MEMS is not just a single thing as an instance it’s a combination of four components like Micro actuators, Micro Sensors, Micro Structure, and Micro Electronics. Furthermore, there are some other components also use for MEMS and NEMS devices like micro or Nano scale gears, actuators, levers, pistons, and motors as well. Sometimes times MEMS may be manufacturing by using NEMS.
MEMS and NEMS Fabricating Methods
There are the most advanced fabricating methods used to fabricate MEMS devices.
- Oxidation
- Ion implantation
- Chemical vapor deposition (CVD)
- Metal sputtering
- Diffusion
- Exciting inventions were developed using those diverse process technologies.
However , many critical issues in MEMS and NEMS fabrication still need to be overcome such issues. These technologies combine these capabilities with highly specialized micromachining processes.
- Bulk etching
- Wire bonding
- Wafer-level packaging
- Complex lithography
MEMS and NEMS Fabricating Materials
In this paragraph, I am going to describe the most common materials used for MEMS device manufacturing. Most of the time manufacturers use semiconductor base materials for MEMS device manufacturing. But for Semiconductor manufacturing highly technical knowledge and huge investment are needed. For instance, the followings are the most common semiconductor raw materials.
- Silicon (Si) / poly-silicon (PolySi)
- Silicon Oxide (SiO2 or SiOx) or silicate glass and Nitride (Si3N4 or SixNy)
- Thin Metal Films of Gold, Nickel
- Aluminum, Platinum, Palladium Chromium, titanium, Titanium-Tungsten, and Permalloy™ (NixFey)
- Indium-tin oxide (ITO)
- Quartz
- Silicon Carbide and Diamond (SiC & Diamond)
- GaAs
- AlN
- 92% Al2O3
- Polyimide PMMA [poly (methyl methacrylate)], polypropylene, polyvinyl chloride, acrylic, and other thermoplastics
- Polymers
- Piezoelectric ceramics
- Piezoelectric Composites (with lead- & lead-free composites)
- Glass and Fused Quartz Substrates
- Gallium Arsenide
- Compound Semiconductors
- Shape-Memory Alloys
- Piezoelectric materials for an instant;
Lead Zirconate Titanate (PZT) is a ceramic-based on solid solutions of lead zirconate (PbZrO) lead titanate (PbTiO3), zinc oxide (ZnO), and PVDF (Polyvinylidene-fluoride)
Advantages of MEMS
There are so many advantages of MEMS Devices
- Reduce the amount of energy and materials needed.
- Enhancing reproducibility.
- Increased operational sensitivity, accuracy, and dependability.
- Economical production (When Produced in Mass)
- Low power is necessary for functioning/operations.
- Compared to its macro equivalent, a device’s component changes are simpler.
- Very little bulk, volume, and size.
- Extremely low power usage as compared to other systems.
- Simple to change or integrate with existing systems.
- Thermal constant is small.
- Has the potential to be very radiation, vibration, and shock resistant.
Where the MEMS and NEMS Fails
We all know mechanical devices are failing with the most common failure modes like creep, and fatigue. Similarly, MEMS Devices also fail due to the same. For instant followings are the examples
- Overload
- Sticking
- Electrostatic Clamping of Gears (Links)
- Static overload
- Delamination
- Creep
- Environmental attack
- Fatigue
NEMS Materials
NEMS are exploring and incorporating materials using smaller dimensions and thinner films including
- Silicon carbide and III–V materials,
- Nitrides,
- Polymers,
- Ceramics,
- Ferromagnetic
- Piezoelectric materials, and even the ultimate thin film: 2D materials such as graphene,
- MoS2 and BN
The Nano devices from 2D materials can be divided into quasistatic and resonant NEMS.
NEMS Fabricating Methods
For the fabrication of NEMS, a variety of materials are used. Diamond materials have enormous promise for use in electronics and biomedicine. The materials based on diamond have a very high stiffness, high thermal conductivity, a wide range of optical transparency, chemical stability, and wear resistance, which expands their applicability for MEMS/NEMS.
Applications of MEMS and NEMS Devices
MEMS- Micro Electromechanical devices and NEMS- Nano Electro-Mechanical device applications are highly interdisciplinary in their current usage. Following are the main application fields with the ongoing latest device developments in the world.
- Automotive industry
- Biomedicine and health care
- Communication
- Defense and security systems
- Information technology
- Avionics and environmental monitoring
The latest development included mechanical sensors, chemical sensors, actuators, micro-optical systems, microanalysis, Bio-MEMS for microscopic surgeries Etc. under the above fields.
Applications of Nano Mechanical Systems
The integrated Nano scale devices known as Nano electromechanical systems (NEMS) combine mechanical and electrical components. NEMS have numerous applications, like;
- Nano actuators and Sensors
- Electromagnetic Detectors
- Quantum Transducers
- Low-Power electronic/Optical Switches
- Relays and memory
- Reconfigurable materials
- Plasmatic devices
MEMS and NEMS in the Automotive industry
This industry has revolutionized with this technology with more enhancing features coming with increasing safety of passengers, improving the durability of automobiles, as well as a low-cost replacement for conventional sensors.
The main current applications of the automobile industry are as follows;
- Tire pressure detection
- Passenger safety purpose
- Rollover and skidding detection
- Electronic stability of control of vehicles
- Rollover and skidding detection
- Electronic suitability of control of vehicles
- Vehicle dynamic controller
- Vehicle navigation systems
- Anti-theft systems
MEMS pressure and flow sensors, accelerometer sensors, gyroscopic, and inclinometers use MEMS technology on a wide scale in the automobile industry.
As an application MEMS pressure is widely used as integrated into the tires of vehicles to measure and monitor the pressure continues, it detects unsafe underinflated conditions more accurately by sensing time-to-time pressure and transmitting tire pressure information to the screen through a radio frequency signals. At a certain pre-determined point exceeding it warns the driver about the condition. This will ensure the safety of both vehicles and passengers while helping to extend the durability of the tire life span
How to use MEMS Devices for Passenger Safety Purposes
Conventional G switches of airbag sensing carry more disadvantages by being less sensitive as well as high cost. The MEMS and NEMS pressure sensors integrated with accelerometer sensors are also designed in the airbag firing systems by detecting sudden declarations more accurately in order to fire the airbag. Compared to installing met of G switches this makes less cost and less weight to the vehicle is also an added advantage. In modern vehicles, there are side airbags installed in vehicle doors, and the airbag firing system is activated by sudden pressure difference which causes deforming the side door This is calculated by MEMS pressure sensors to fire upside airbag systems.
The multiplexer which accelerometer, impact sensors, wheel tachometers, gyroscopes, and brake pressure sensors integrated MEMS/NEMS system allows more accurate sensing with the highest sensitive airbag firing at the shortest possible time periods
Exhaust Gas Recirculation System
Vehicle exhaust gas recalculating systems are increasingly using MEMS pressure sensors. Nitric oxide, a harmful gas created during combustion, is released less frequently when it is recirculated into the combustion engine. As a result, the recirculation system’s valve at the combustion exit is managed by MEMS pressure sensors. High exhaust gas emissions can be detected by pressure sensors at the combustion engine’s exit, which permits the recalculation valve to open wider and allow for more recirculation back to the combustion engine.
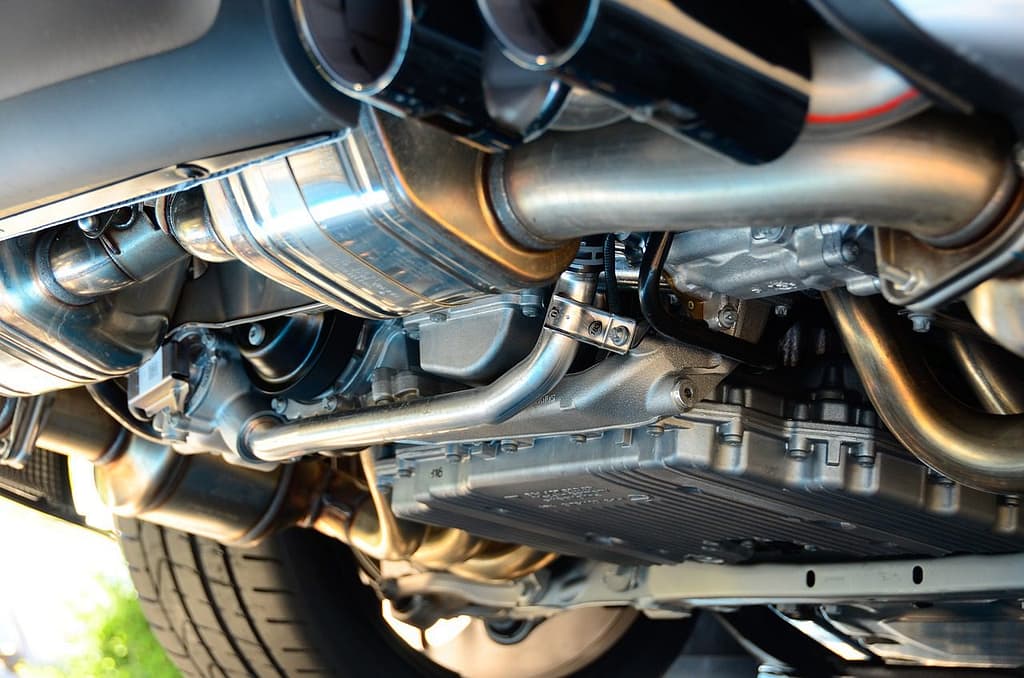
Vehicle Navigation Systems
MEMS gyroscope system combined with the GPS navigation system allows finer navigation according to the precise vehicle location. Conventional GPS system’s signals may block by buildings and physical barriers, but this system integration allows enhanced smoother navigating.
Blood pressure measuring systems
One of the most used is invasive blood pressure monitoring by using MEMS pressure sensors, as well as it comes in lower manufacturing cost compared to the conventional blood pressure monitoring systems. During the surgeries, the micro size of both sensors preserves a more visualizing area for the surgeon’s surgical field. Micro size comes easy to sterilize as well.
Pressure data is transmitted in a radio frequency signal and is digitalized by analog to digital converter.
Really appreciate you, taking the time to read the article about the difference between MEMS and NEMS. So keep in touch with MechHeart and feel free to add some comments here and share your knowledge with us.
0 Comments